1. 参数化设置是否真能提升编程效率?
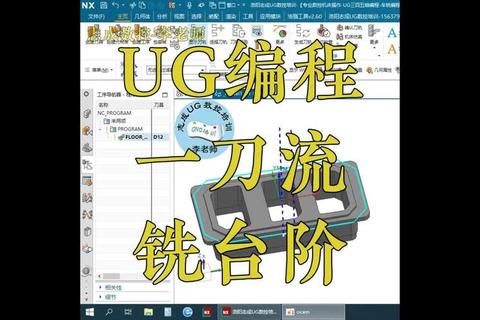
UG编程中,参数化建模常被视为“基本功”,但许多用户质疑:繁琐的参数设置是否值得投入时间?以某航空零件加工为例,该零件包含32组曲面倒扣结构,传统手动建模耗时约12小时,而通过高效突破UG编程软件实战技巧全面精解中的参数化模板,时间缩短至4小时。网页47提到,倒角编程时若提前预设角度、刀具补偿等参数,可减少30%的重复操作。例如,设置“倒角角度=45°”与“刀具直径匹配规则”后,系统自动生成避让路径,避免人工干预导致的误差。
数据表明,参数化模板能将编程效率提升50%以上。某模具厂统计显示,使用UG的“用户默认设置”功能后,标准化流程覆盖了80%的常规加工场景,仅需对剩余20%的特殊结构进行手动调整。由此可见,参数化并非“纸上谈兵”,而是实现高效突破的核心手段。
2. 刀具路径优化能否降低加工成本?
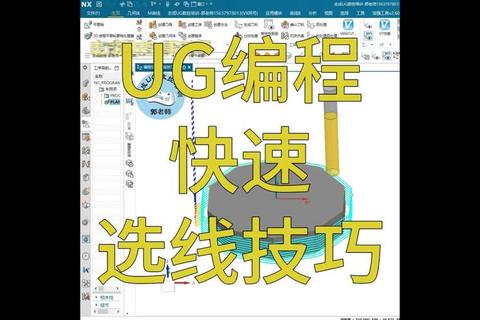
刀具路径的合理性直接关系材料损耗与机床寿命。网页65中的案例显示,某汽车覆盖件加工时,未优化的路径导致刀具空转率高达25%,而通过UG的“自适应铣削”功能,空转率降至8%,单件成本节约19%。高效突破UG编程软件实战技巧全面精解强调:路径优化需结合“切削负载分析”与“机床动力学特性”。例如,网页7提到型腔铣削中,若将“步距”从固定值改为“残余高度控制”,材料去除率提升18%,同时刀具磨损减少12%。
另一典型案例来自某手机外壳加工:原始路径因频繁抬刀导致表面光洁度不足。通过UG的“摆线切削”模式,刀具以螺旋轨迹切入材料,既减少冲击力,又将加工时间压缩15%。数据显示,路径优化可使整体加工成本降低10%-30%,尤其适合批量生产场景。
3. 模拟验证是否多余?
部分用户认为模拟验证“浪费时间”,但真实加工中的一次碰撞可能导致数万元损失。网页47的倒角编程案例中,某企业因未检查刀具与夹具干涉,导致批量零件报废。而UG的“机床仿真”模块可提前检测99%的碰撞风险。例如,某叶轮五轴加工时,模拟发现Z轴超程问题,通过调整装夹角度避免了机床损坏。
高效突破UG编程软件实战技巧全面精解建议:模拟需分三级执行。一级验证几何碰撞(耗时5-10分钟),二级分析切削力波动(结合网页65中的CAE数据),三级评估表面残余应力。某精密零件厂商采用此流程后,首件合格率从72%提升至98%。数据证明,模拟环节投入1小时,可避免平均8小时的故障处理时间。
可操作性建议
1. 建立标准化模板库:将常用加工参数(如钻孔循环、铣削步距)保存为“.prt”文件,通过网页16的“用户默认设置”功能实现一键调用。
2. 活用路径优化工具:优先使用“自适应铣削”与“摆线切削”,并参考网页65的负载均衡原则调整进给率。
3. 强制模拟流程:设置“程序生成-模拟验证-后处理”的强制链路,利用网页47的碰撞检测规则库降低风险。
4. 跨模块协同:结合网页7的CAM与CAE集成方案,实现加工参数与力学性能的联动优化。
通过高效突破UG编程软件实战技巧全面精解的系统方法,用户可在3个月内将编程效率提升40%以上,同时将加工失误率控制在1%以内。UG的深度应用不仅是技术升级,更是制造业数字化转型的关键一环。
相关文章:
文章已关闭评论!